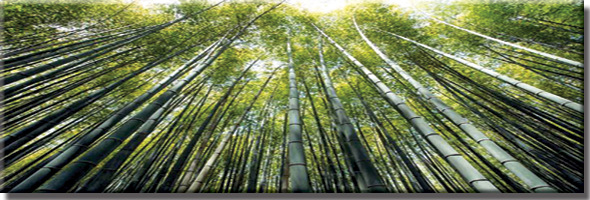
Engineered bamboo has just taken an enormous production leap, from hours to just minutes.
That’s how fast a local machine is able to process engineered bamboo.
Engineered bamboo is so-called because it is made of composite materials from bamboo: strands, fibers, strips or slats, woven mats or flattened fibers and particles that are bound together when they are pressed with adhesive.
There is a huge potential for engineered bamboo. Only about 10 local companies make engineered bamboo products on a small, per-order scale. However, Executive Order 879 requires that one-fourth of all desks and furniture in public schools be made of engineered bamboo.
And that’s just for public schools. In other places, engineered bamboo is used in making panels, floors, furniture and handicrafts that are often stronger and less prone to warping than equivalent solid wood.
The hot press machine, being rolled out by the Department of Science andTechnology’s Forest Products Research and Development Institute (FPRDI), is designed to cut the production time of engineered bamboo products.
“With our newly developed machine, we were able to press bamboo boards in only 5 to 8 minutes, compared to the current cold pressing time of 6-8 hours,” saidengineer Edward Paul Marasigan of FPRDI.
“The machine can be operated using both electricity and charcoal as heat source, and makes boards with the same quality regardless of heat source and type of glue used. Fabrication cost is around P150,000, a cost comparable to the price of a cold press machine available in the market,” he said.
A hot press machine uses heat and glue to press – and bond – the bamboo materials together; the heat makes the glue work faster so the press time is shorter. In comparison, a cold press works on pressure alone, bonding the glue and bamboo materials together for hours.
FPRDI puts the global market for bamboo products at $12 billion, a considerable amount of that from engineered bamboo; the global market could be worth as much as $20 billion by 2020.
“Although still immature and bugged by various problems, the Philippines now has its own engineered bamboo industry,” said Dr. Romulo Aggangan, FPRDI director. “In time it will be able to meet the needs of local clients or even capture a slice of the global market.”
These are not easy days for the young industry, noted Dr. Rico Cabangon of FPRDI. It does not have enough supply of bamboo poles; the quality of poles is low and the price high; glues are expensive; and producers do not have the means to buy high-capacity machines.
To meet the projected annual demand of 312,000 school desks and other saleable products such as panels, flooring, decors and high-end furniture, about 10,000 hectares of plantations must be established using the right bamboo species.
The most common species used in making engineered bamboo are kawayantinik (Bambusablumeana), giant bamboo (Dendrocalamus asper), bolo (Gigantochloalevis), botong (Dendrocalamuslatiforus) and bayog (Bambusamerrilliana).
There are plus points, saidCabangon, pointing as example the National Greening Program which lists bamboo as a priority reforestation species. R&D also helps: the FPRDI has developed the bamboo flattening machine and the bamboo veneer lathe specifically for engineered bamboo.